Table of Contents
Introduction
Scientific management means knowing exactly what you want men to do and seeing that they do it in the best and cheapest way.
Taylor emerged as the ‘Father of Scientific Management’. Taylor worked in The Bethlehem Steel company where he achieved a three-fold increase in productivity by application of these scientific management principles. Therefore, it is important to discuss these principles:
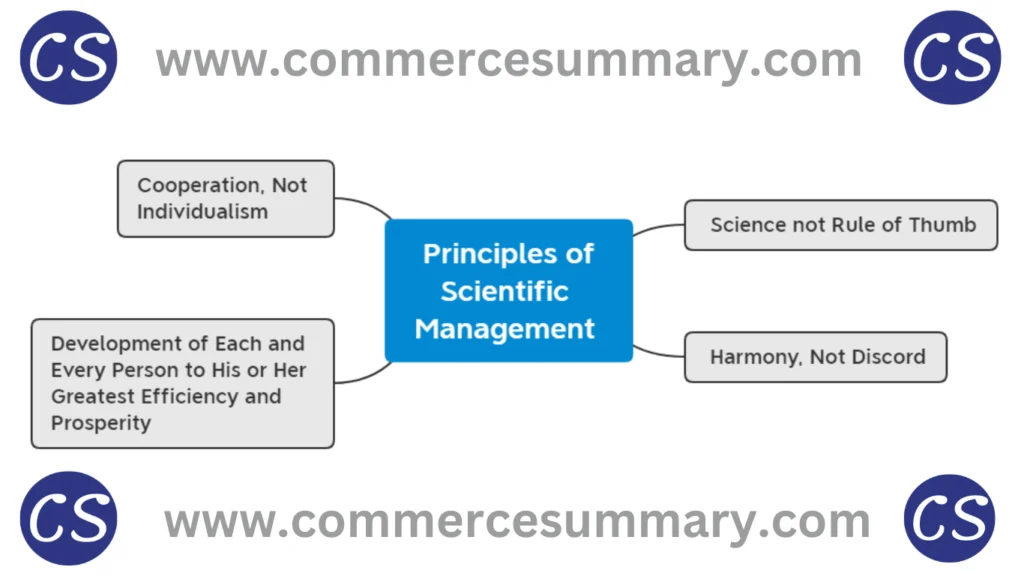
Principle 1 – Science not Rule of Thumb:
Taylor’s principle of “Science, not rule of thumb” means using scientific methods and data to make decisions instead of relying on intuition or traditional practices.
In the past, many businesses and industries used “rule of thumb,” which means making decisions based on personal experience or customary practices. However, Taylor believed that this approach could lead to inefficiencies and inconsistencies.
Instead, he prescribed using scientific techniques, such as time and motion studies, to analyse tasks and identify the most efficient ways of doing them. By gathering data and applying scientific methods, businesses could make more informed decisions and improve their processes to achieve better results.
For example, in a factory, instead of relying on workers’ guesses for the best way to assemble a product, Taylor’s approach would involve conducting time and motion studies to determine the most efficient sequence of steps. This scientific approach would lead to increased productivity and reduced wastage, benefiting both the workers and the company as a whole.
Principle 2 – Harmony, Not Discord:
Taylor’s principle of “Harmony, not discord” means promoting cooperation and positive relationships between workers and management in the workplace.
Taylor believed that a harmonious work environment is essential for maximising productivity and efficiency. When there is a sense of unity and understanding between employees and their supervisors, it creates a more positive and productive atmosphere.
Instead of conflicts and disagreements between workers and management, Taylor emphasised the importance of collaboration and mutual respect. By promoting a culture of teamwork and open communication, organisations can achieve better results and work towards common goals.
For example, in a company, if management values and respects the opinions and ideas of their employees, it can lead to increased employee satisfaction and commitment to the organisation’s success. On the other hand, if there is constant conflict and mistrust between workers and management, it can lead to low morale and decreased productivity.
Principle 3 – Cooperation, Not Individualism:
Taylor’s principle of “Cooperation, Not Individualism” tells the importance of teamwork and working together rather than focusing mainly on individual efforts.
Taylor believed that the most effective way to achieve success in the workplace is through cooperation and collaboration among employees. Instead of working in isolation, individuals should come together and contribute their skills and expertise towards a common goal.
By promoting a culture of cooperation, employees can pool their strengths, complement each other’s abilities, and tackle challenges as a unified team. This can lead to increased efficiency, better problem-solving, and a more productive work environment.
For example, in a project-based organisation, if team members work together and share their ideas and knowledge, they can complete tasks faster and with higher quality. On the other hand, if individuals work independently without communicating or cooperating, it can lead to misunderstandings, duplication of efforts, and slower progress.
Principle 4 – Development of Each and Every Person to His or Her Greatest Efficiency and Prosperity:
Taylor’s principle of “Development of Each and Every Person to His or Her Greatest Efficiency and Prosperity” means that every individual in the organisation should be given the opportunity and support to reach their highest potential in terms of skills, productivity, and overall well-being.
Taylor believed that when employees are given the chance to develop their abilities and talents to the fullest, it benefits both the individual and the organisation. By investing in the growth and prosperity of each person, businesses can achieve higher levels of productivity and success.
This principle advocates for providing employees with the necessary training, resources, and encouragement to excel in their roles. It also involves recognizing and valuing each person’s unique strengths and helping them find their best fit within the organisation.
For example, in a company, if employees are offered opportunities for professional development, such as workshops, training programs, or mentorship, they can enhance their skills and knowledge, leading to improved performance and job satisfaction. Additionally, when employees feel supported and valued, they are more likely to be loyal to the organisation and contribute positively to its success.
Techniques of Scientific Management
F.W Taylor (Frederick Winslow Taylor) had given the principles of scientific management that’s why he was popularly known as “Father of Scientific Management”. He had also given some techniques to practice scientific management in any company. These techniques are based on the various experiments he had conducted during his career.
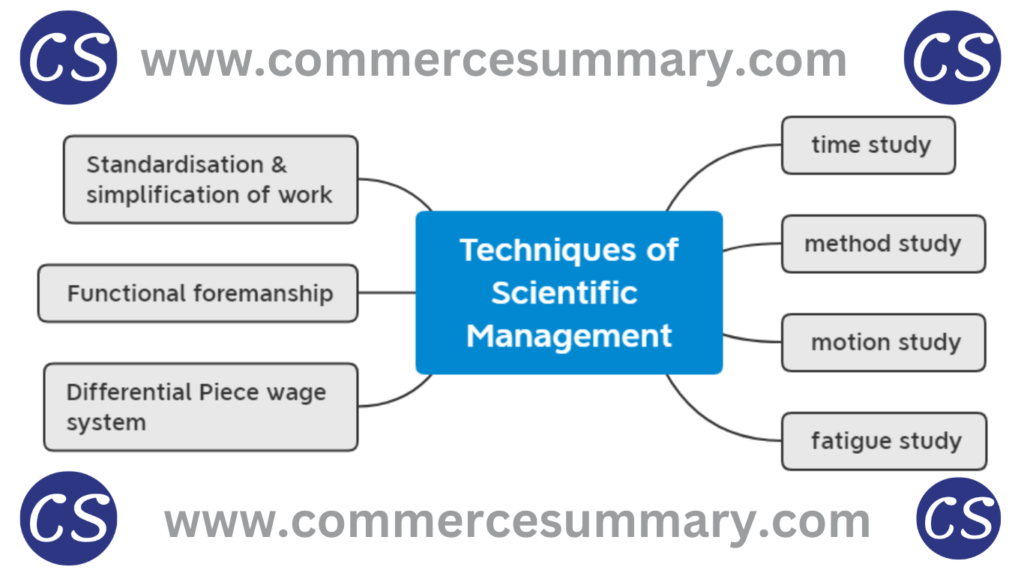
NOTE – TRICK TO REMEMBER ALL TECHNIQUES OF SCIENTIFIC MANAGEMENT
“To Make My Face Smile Do something Funny”
T – time study
M – method study
M – motion study
F – fatigue study
S – Standardisation & simplification of work
D – Differential Piece wage system
F – Functional foremanship
Now let us Briefly discuss this one by one:-
1.Time study –
It determines the standard time taken to perform a well-defined job. The objective of time study is to determine the number of workers to be employed, frame suitable incentive schemes & determine labour costs.
For example:- on the basis of several observations it is determined that standard time taken by the worker to make one cardboard box is 20 minutes. So in one hour he will make 3 boxes. Assuming that a worker has to put in 8 hours of work in a shift and deducting one hour for rest and lunch, it is determined that in 7 hours a worker makes 21 boxes @ 3 boxes per hour. Now this is the standard task a worker has to do. Wages can be decided accordingly.
2. Method Study –
The objective of method study is to find out one best way of doing the job to maximize efficiency in the use of resources and to reduce cost of production and to maximizing quality and satisfaction of customers.
For example:- For designing a car, the assembly line production would entail deciding the sequence of operations, place for men, machines and raw materials etc. All this is part of method study.
3. Motion Study –
Motion study refers to the study of movements like lifting, putting objects, sitting and changing positions, etc., which are undertaken while doing a typical job.
Through motion study , it is possible to find out:
(I) Motions which are productive
(II) Motions which are incidental (e.g., going to stores)
(III) Motions which are unproductive.
And we can use videography to identify these different types of motion.
- The main aim of motion study is to eliminate the unproductive or unnecessary movements so that it takes less time to complete the job efficiency.
NOTE:- Work study – It ensures the maximum production at minimum cost and getting best contribution from every factor.
Work-study =Time study + Motion study + Method study + Fatigue study.
4. Fatigue Study –
a fatigue study is a technique used in scientific management to understand and address the physical and mental tiredness experienced by workers during their tasks. Let’s explore this technique with an example to make it easier to understand.
Example of Fatigue Study:
Imagine a manufacturing company that produces electronic devices. The assembly line workers are responsible for assembling various components of the devices throughout their shifts. However, as the workday progresses, some workers start to feel tired, and their performance may decline, leading to mistakes and reduced productivity.
To address this issue, the company decides to conduct a fatigue study. They hire experts to observe and measure the workload of the assembly line workers and their rest intervals. The study also assesses the physical and mental demands of the assembly tasks.
During the study, the experts find that the workers have long periods of continuous work without sufficient breaks. This extended work without rest is causing fatigue, leading to errors and decreased efficiency.
Based on the findings of the fatigue study, the company implements the following changes:
- Workload Distribution: They reorganize the assembly line tasks to distribute the workload more evenly among workers. This helps prevent some employees from being overwhelmed with excessive work while others have lighter loads.
- Scheduled Breaks: The company introduces scheduled short breaks for the workers at regular intervals. These breaks allow the workers to rest and recharge, reducing the impact of fatigue on their performance.
- Ergonomic Improvements: The company invests in ergonomic improvements in the workplace to reduce physical strain on the workers. This includes providing comfortable seating, adjustable workstations, and proper tools to make tasks easier and less physically demanding.
As a result of the fatigue study and the implemented changes, the assembly line workers experience less fatigue throughout their shifts. They can perform their tasks more efficiently, with fewer errors and higher job satisfaction. The company benefits from improved productivity and quality of their electronic devices.
5. Standardisation & simplification of work –
Standardisation means setting up standards for size, type, weights, measures and quality of products.
Simplification means giving emphasis on the elimination of unnecessary sizes & types of products.
As more varieties mean more inventory, more types of machinery, more labour and cost etc. i.e. more headache.
So by implementing standardisation and simplification of work techniques we can improve the quality of the product and reduce the production cost.
For example:- a can manufacturing company that manufactures can for different drinking items like fruit juice and coke etc reduced its varieties from 200 to 32 and got effective and efficient results.
6. Differential Piece wage system –
It is a technique which differentiates between efficient & non efficient workers. Basically it rewards the efficient workers and motivates the less efficient ones to improve their efficiency.
In this system , there are 2 piece wage:
- One for those workers who produced according to the planned output or more than that.
- Another for those who produce less than the planned output.
Taylor insist that This difference in the wages of this system is enough for the inefficient workers to get motivation to perform better.
For example – suppose planned output per worker per day is 100 units
Wage rate I – ₹4 per unit is given as wages for output less than 100 units.
Wage rate II – ₹5 per unit is given as wages for output more than 100 units.
Now suppose there are two workers – Ram & Shyam. Ram produces 80 units / day & Shyam produces 120 units / day.
Ram wage per day = 80 * 4 = ₹320
Shyam wage per day = 120 * 5 = ₹600
So, difference in units produced = 40 units
Difference in wages = ₹280
Therefore, According to F.W Taylor , this loss will act as a strongest motivator for Ram to reach the planned output next day.
7. Functional foremanship –
In the factory system, the foreman represents supervisor.
Functional foremanship is an extension of the principle of ‘division of work & specialization’ to the shop floor.
functional foremanship is a technique which aims to improve the quality of supervision at shop floor by putting a worker under 8 specialist foreman in the process of production.
Foreman should have intelligence , education, tact, judgement , special knowledge , energy , honesty & good health.
All these qualities cannot always be found in one human being therefore Taylor proposed 8 specialists in the following below given manner.
- Planning Incharges :
1. Disciplinarian – to ensure discipline and enforcement of rules and regulations among the workers.
2. Instruction card clerk – responsible for drafting instructions for the workers.
3. Route Clerk – to specify the exact sequence and route of production.
4. Time and cost clerk – to prepare time and cost sheet for the job.
- Production Incharges :
1. Gang boss – responsible for keeping tools and machines ready for operation.
2. Inspector – to check quality of work.
3. Repair boss – to ensure proper working conditions of tools and machines.
4. Speed boss – responsible for timely and accurate completion of job.
Note:- Trick to Remember this 8 Specialist is – “DIRTY GIRLS” . here ‘Y’ in dirty and ‘L’ in girls doesn’t signifies anything.
Disclaimer – this is a just a trick to make you remember the things. The author has no intention for hurting the sentiments of girls.